BUILD-TO-PRINT: MANUFACTURING AND ASSEMBLING ACCORDING TO THE CUSTOMER’S TPD
SERIES PRODUCTION
In Built-to-Print production, the responsibility for the product design lies primarily with the customer. Our focus, in this case, is on efficiently manufacturing, assembling, and testing the systems in series within the agreed QLTC parameters (Quality, Logistics, Time, Cost).
TPD QUICKSCAN
A COMPLETE TPD IS THE BASIS FOR SUCCESS
The customer's Technical Product Documentation (TPD) is the starting point for a Build-to-Print project. While this dossier provides a lot of information about the desired product, it does not cover everything. The information is often based on a specific (internal) production chain and is therefore prone to interpretation issues. We perform a quickscan to check the completeness and suitability of the provided information for production.
After the scan, we determine the most effective route to series production. It is essential to eliminate any interpretation issues, as a well-defined TPD is the basis for achieving a competitive price.
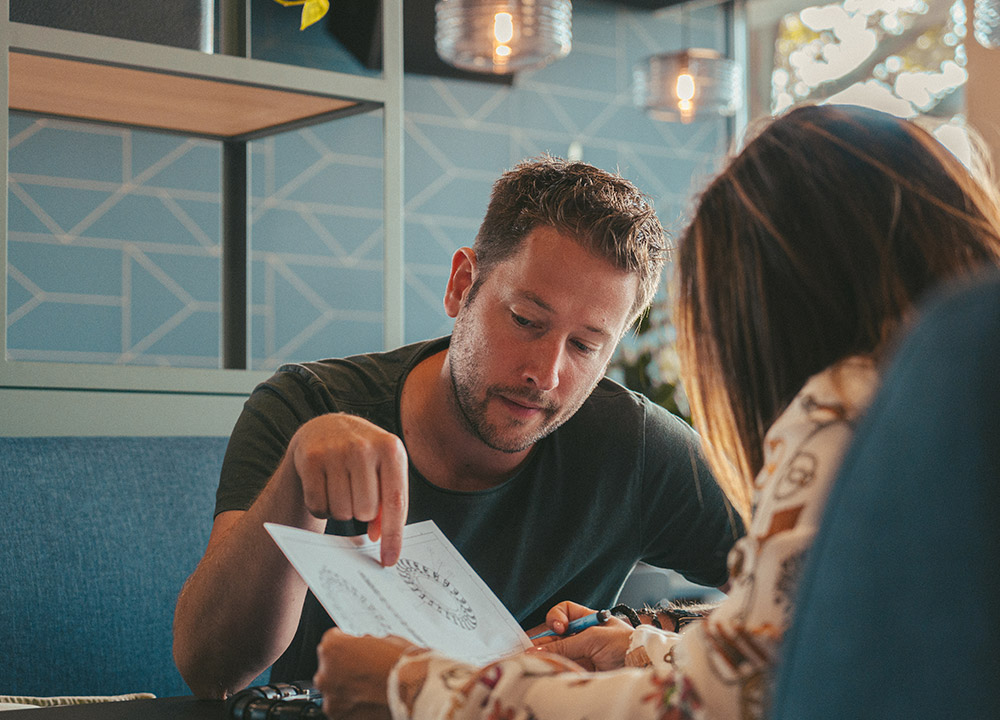
MTA TAKES THE LEAD
NPI - New Product Introduction
Based on the validated TPD, a project plan is created that includes the QLTC parameters. At the same time, the production process is prepared. This involves setting up the production concept, organizing the supply chain, and ensuring that all processes are ready for future scaling to series production.
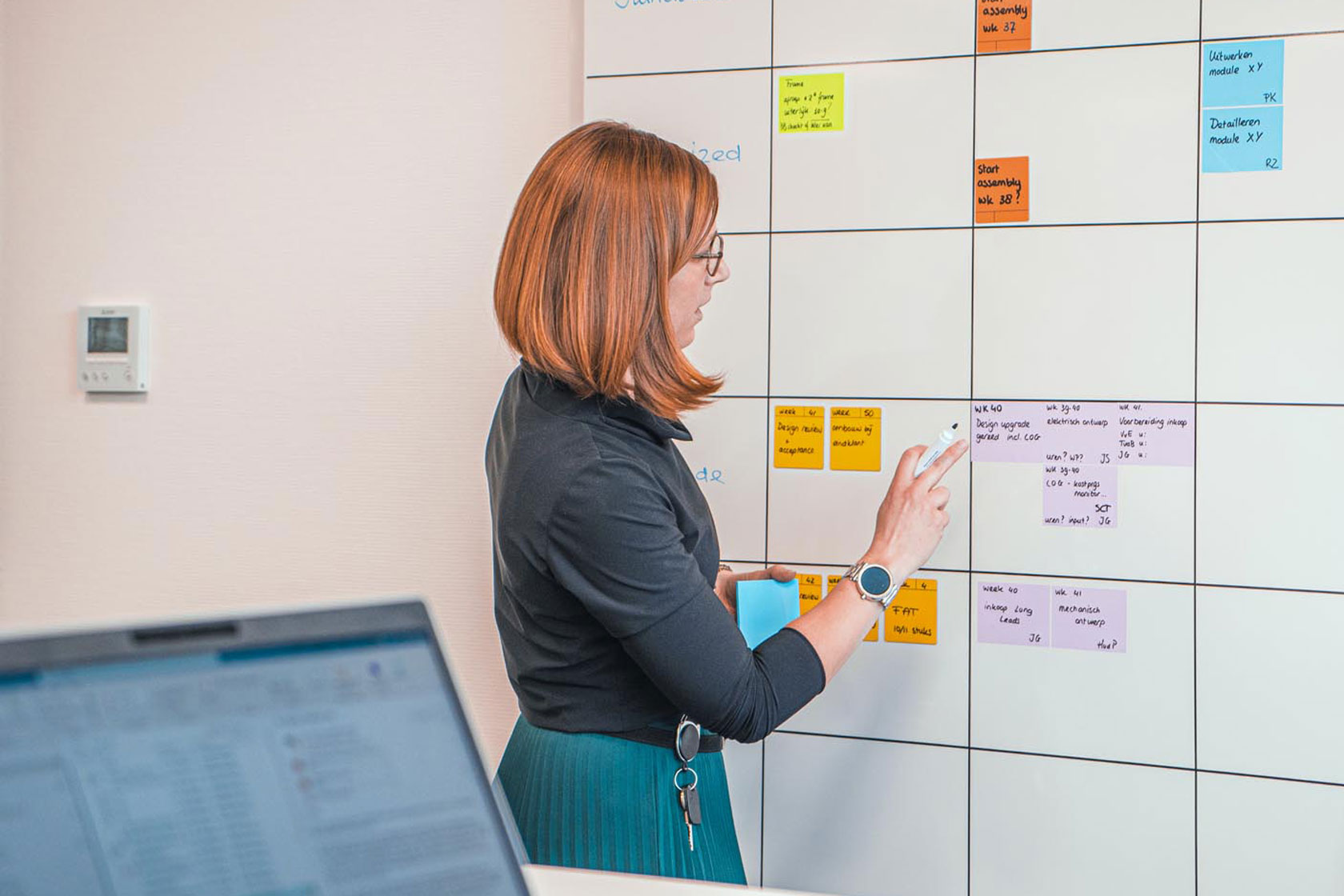
MTA PRODUCTION CONCEPTS
Choosing the right production concept is crucial and defines how we structure the supply chain. Our assembly floor has a flexible layout, allowing us to set up a dedicated production area optimized for each project. Depending on the situation, we choose from one of these three production concepts:
SCALING UP TO SERIES PRODUCTION
System Supply
After completing the First Article Inspection (FAI) and approval of the initial batch, we scale up production. Internally, we ensure a smooth handover to the System Supply team for series production.
From this point on, the Order Management Center (OMC) takes control. Based on the QLTC parameters, the OMC manages, coordinates, and monitors the production process for subsequent series.
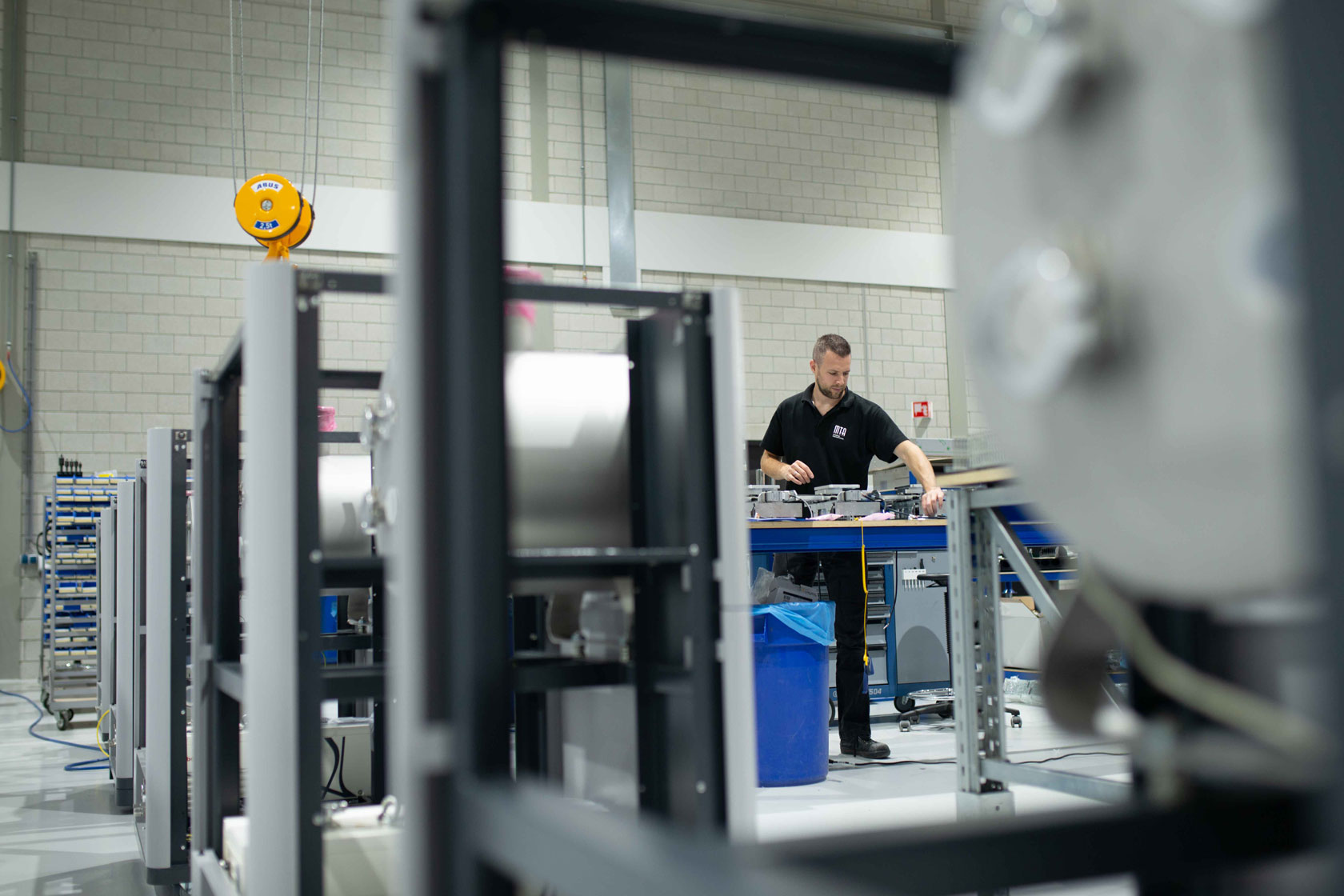
Our specialists for series production
Supply Chain Team
Organization and management of the supply chain
- Flexible, reliable international supply chain.
- Not restricted in technology selection.
- Not dependent on production capacity in the Brainport region.
- We are a top-5 customer with our production partners.
Production Competence Center
In-house expertise in modern manufacturing techniques.
- Knowledge base of manufacturing techniques and manufacturability.
- Design optimizations.
- Knowledge transfer to the supply chain.
- Quick Response Manufacturing.
- Fast lane for prototype production or the start-up of complex components.
Order Management Centre
Preparation and coordination of the production process based on QLTC.
- Translating customer orders into production dossiers.
- Planning and coordination of internal and external activities.
- Procurement and scheduling of components.
- Project coordination and problem-solving.
- Project setup in ERP software ISAH.
- TPD management.
Logistics
Inventory control and management of goods flow.
- Over 700 pallet positions.
- Over 6,000 shelf locations.
- 1,800m² warehouse space.
- Proprietary scanning application.
Assembly
Assembly and testing of machines and systems.
- Climate-controlled production area of over 2,000 m²
- Capacity of approximately 1,000 hours per week, flexibility + 25%-35%
- Highly skilled assembly technicians.
- Flexible layout of the assembly floor.
- Quality assurance using our proprietary Assembly Quality System (AQS).
DESIGN WITH PRODUCTION IN MIND
Industrialization
Within our one-stop factory, we have all the competencies needed to execute an industrialization process.
An industrialization process allows us to shorten lead times, minimize waiting times, and reduce manufacturing costs.
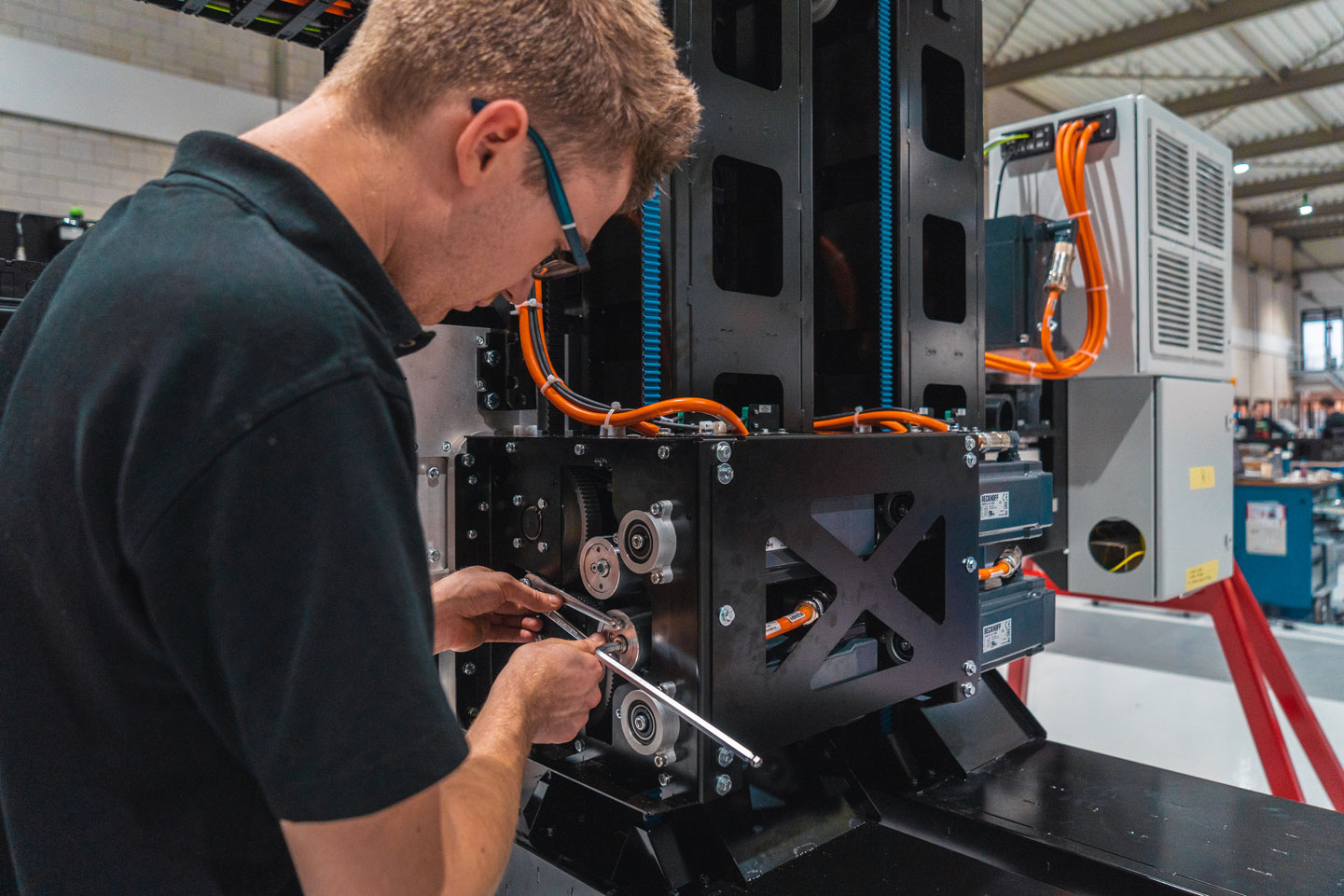